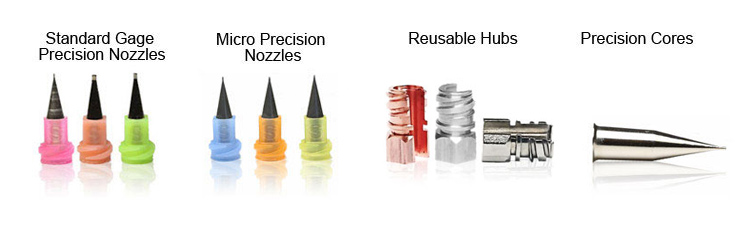
Product Design
Exceptionally accurate nozzles can be assembled from cores with walls of varying and constant thickness at low cost. Nozzles can be manufactured with an inside diameter as small as 0.002 inch. This process enables creation of the conical shape through a series of progressive die punches. Formation of liquid dispensing nozzles using this technique is wholly unique, allowing the creation of shapes that are not possible through typical machining processes or other methods. Another feature is the ability to have a highly polished surface in the interior because it is formed out of a flat sheet of metal. This process causes internal stress in the metal from plastic deformation forcing metal properties to change through cold work and subsequently work harden, making the nozzle more rigid and resistant to deformation.
Thinner walls provide less facial area at the exit aperture upon which fluid can adhere, resulting in a cleaner break off of the dispensed liquid. The thinner wall also results in the smallest difference between surface areas on the exterior as opposed to the interior. This reduces surface tension forces, which direct the fluid to accumulate on the exterior of the nozzle. Thus, more liquid tends to be held on the interior of the nozzle, improving both speed and accuracy of the automated dispensing process. Coatings can be applied to the nozzle core to optimize performance for specific applications.
Nozzle construction material should have good heat transfer characteristics if thermal performance is determined to be important for the application. Adding heat to viscous adhesives and sealants will produce a dramatic reduction in viscosity. Reducing viscosity can enhance dispensability of the liquid. Thinner walls also enable a more uniform and rapid thermal response promoting more efficient heat transfer to the fluid.
Product Design Characteristics List
- Thermal transfer
- Lower flow rate variance
- Nozzle tip placement closer to the proximity of the electrical components
- High repeatability at high rates of flow
- Improved accuracy of the dispensed volumes (relates to the unique architecture, enabling clean fluid breaks from the nozzle)
- Superior resistance to nozzle deformation or bending
- Extraordinarily small center line variation tolerance or run out
- Ultra Thin Dispense Tip Walls
- Enables the use of smaller outside diameter dispense tips without reducing inside diameter fluid flow rates or flow channel dimensions
- Reduces fluid dispense distance from chip devices
- Allows easier access in tight geometries
- Thermally Conductive Composition
- Provides superior thermal process management
- Enables higher through puts and yields in production applications
- Cone Design
- Modeled to be the most ideal passage for transfer of fluids
- Unobstructed fluid path
- Increases flow rate capability
- Standard ISO 594 6% Taper
- Coatings can be applied
- Full 360˚ Thread
- Different hub styles
- Greener - 94% less disposed waste by using a reusable hub